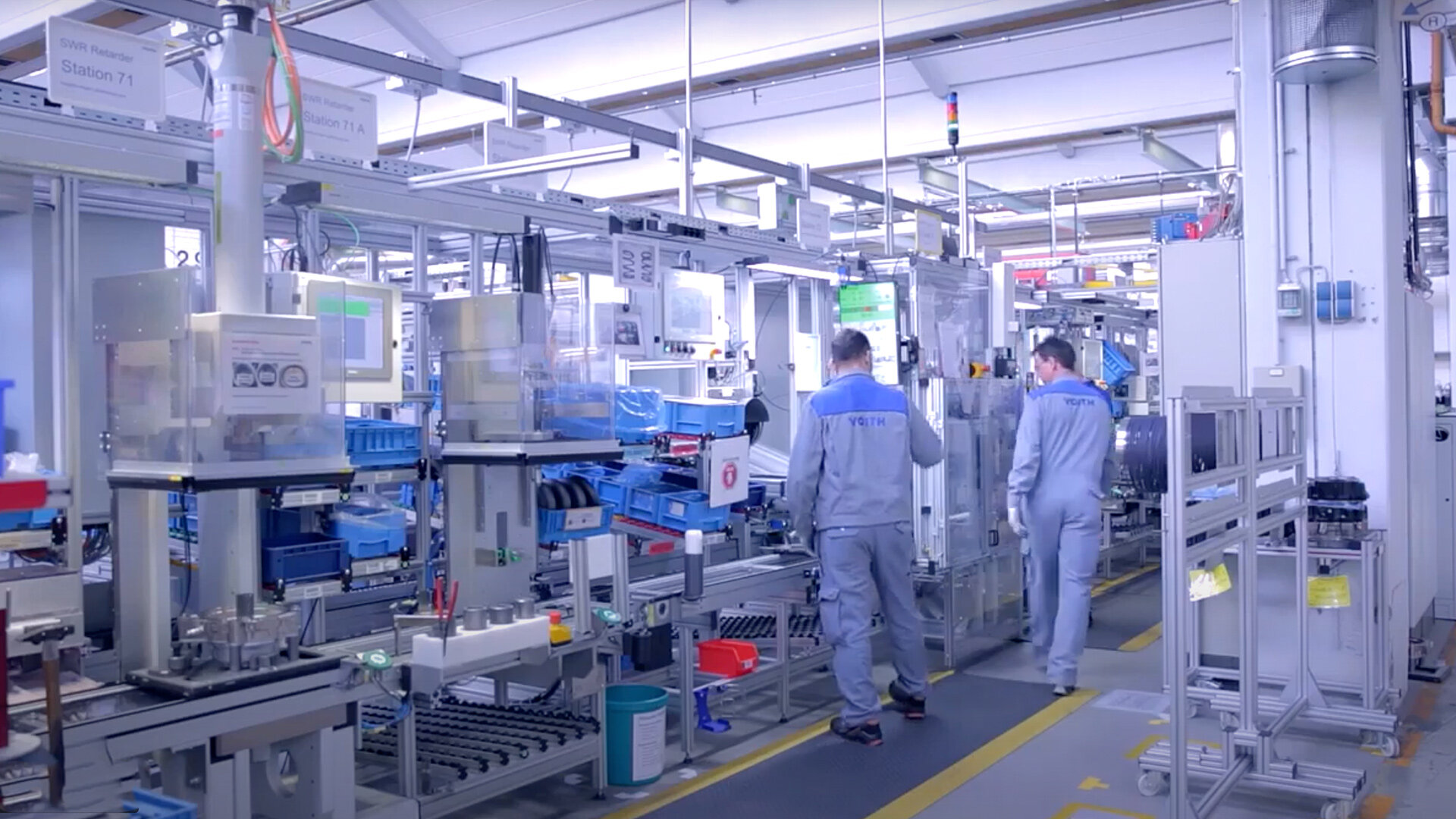
Success Story
Voith Turbo
Smart Interface Application for SWR Aquatarder
MISSION
The customer-specific production of state-of-the-art and low-wear brake systems requires a high degree of flexibility with regard to the creation of variants and changes during the production process. Delivery dates and high quality standards are important to be adhered to. The resulting challenges often lead employees to their performance limits. Real time interactive digital planning and optimization systems help to avoid errors and productivity losses despite the high time and cost pressure.
Solution and Work Process
We started with a project called „Smart interface to deploy efficiently employees with impaired abilities in assembly lines”. The better communication and interaction by using smart devices improved the working conditions and the capacity utilization at the same time.
Production Planning: simulation-based mapping of assembly processes under consideration of all dynamic interactions
Work Orders: optimization of work order sequences to minimize use of jumpers
Production Allocation: real time workers’ allocation depending on their qualification
Personal Deployment: high reactivity by considering available workforce prior to each shift and continuous rescheduling triggered by shop floor feedback.
Results
Simulation of new processes
Production increase by 15% - maximized operating grade of line
20% faster reaction time in case of problems
Reduction of lead time by optimized assignment of specialists
Keep competencies of performing employees